Guide for online sellers: the Picking List

The order preparation process is one of the most complex and expensive operations of a warehouse. The evolution of consumer habits pushes to prepare orders always faster. Orders are getting smaller, but more numerous.
To optimize flows and improve the overall productivity of the center, the picking list is a great asset to prepare orders faster, with less errors.
Table of Contents
The Picking List: a technical means of order picking
What is the Picking List?
In logistics, “picking” is the operation of taking and collecting the items in the quantity specified by the order before shipping it.
To carry out this task, the preparer receives a list specifying the location of the product in the warehouse, its number, its designation and the quantity to be collected.
Once the picking list is generated, the order processing can start. This method helps to better organize order picking and speed up the process.
Which type of list to choose?
A picking list looks like your customer’s shopping cart before he or she proceeds to check-out. Thus, it can count one or more articles.
- The printed list
This is usually a printed list on paper or a list of labels. Before integration software, mobile technology or WiFi, the warehouses used a paper version of these lists. Each picking list was then distributed to each order picker.
- The digital list
The automation of the system allows today to have a list generated by an e-commerce application. This will then be sent to the pickers on a digital terminal. This method implies that tablets or laptops are used in the warehouse. Thus, the details of each order are sent and assigned to each order preparer who follows clear instructions for a more efficient process.
The advantages of the picking list
Young businesses often have low sales volume with a small catalog of products. Stocks and orders are then directly managed by the company.
The picking list becomes essential as the volume of your stock increases as well as the volume of your sales. Moreover, if you chose to sell your products on different Marketplaces and your product catalog is varied, the picking list can reduce the number of errors and accelerate order preparation.
These advantages may seem minimal in the order preparation process, but they have a real impact on your supply chain. The picking list makes it possible to process sales orders more efficiently, accurately and on a large scale. In fact, it facilitates product localization in the warehouse and explains in detail the quantity and designation of the ordered products.
How to optimize the logistics of your E-commerce
6 essential information to include in your Picking List
The items in your picking list vary depending on your warehouse, your company, and your products. If you do not use a warehouse management system that generates your picking lists, you will need to create a list template. To do this, the most practical and complete tool is Excel, which allows you to create an inventory.
- Customer information
Order pickers do not need this information, but may become necessary later in the order preparation process. Packing or labeling agents must actually verify the customer’s name and delivery address as a quality guarantee.
- The date and time of the order
Several e-commerce sites offer to deliver in the day if the order was placed before a certain time. If you are in this case, your team will want to be able to follow the date and time of each order to prioritize the most urgent orders.
- The order number
It is associated with each picking list allowing the customer to have a reference of his order in case of problem (for example, for a return or a package not delivered). Digital picking lists offer the advantage of greater transparency and visibility throughout the entire process.
- The location of the product in the warehouse
Order pickers must have the maximum of information to find in the warehouse the ordered article. This is why the exact location, or the most specific possible, helps to speed up the procedure. In addition, the warehouse must have clear and visible signals so that pickers can navigate the shelves more easily.
- The product SKU
The SKU (Stock Keeping Unit) is a unique identifier that designates a specific article differentiable from other items in stock through criteria such as brand, color, size. Some orders may have more than one SKU code.
- Product description
It happens that two different articles are very similar. Thus, adding a description or a picture of the product is a way to ensure that the order picker has found the right article.
4 common methods of order preparation
The various methods all aim to optimize the operational efficiency of the order pickers and vary according to the configuration of the warehouse, the available staff or the volume of orders.
- Collection by article
This is the most common and basic method of taking products in a warehouse. Pickers simply receive orders as they arrive. This method is simple to implement, especially for small businesses that have few products.
- Batch picking
This method is characterized by the simultaneous collection of several units of the same SKU code for different orders. Its main advantage is that it reduces the travel time of operators within the warehouse.
- Zone picking
In order to optimize itineraries and avoid crowds or excessive traffic in the aisles of the warehouse, several orders are assigned to the order pickers according to the location of the goods.
- Wave picking
This method combines the use of the two previous methods. It mainly consists of grouping orders according to logistical criteria, such as the delivery route or the degree of dispatch priority. Then each picking wave is assigned to an operator to collect the products that are part of the same route.
Increase the impact of your e-commerce with ShippyPro
We can think that attracting new customers is the most difficult task for an e-commerce company. However, order preparation and management of logistics services are equally important.
The picking lists play a fundamental role in maximizing the working time of the order pickers in the warehouse, but also in reducing costs. ShippyPro allows your e-commerce to connect with the largest network of carriers and take advantage of shipping data.
Simple and intuitive, the ShippyPro platform saves you valuable time by automating your shipments. Thus, you can create your own shipping routine, generate return labels and choose the best carrier with the shipping rate comparator.
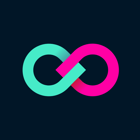
ShippyPro is the complete shipping software for online and offline retail. With Label Creator, Track & Trace, Easy Return and Analytics features, our software simplifies your shipping operations. ShippyPro integrates with over 180 carriers and 80 sales channels, making it compatible with a wide range of products and use cases.