Minimum stock levels for e-commerce: strategies for success

There are many things that need to be kept in mind when running a successful eCommerce business, and making sure you always have enough stock available is one of them.
Maintaining minimum stock levels is a fundamental stock control method, and failure to do so can cause problems with your customers and supply chain. Here is why maintaining a minimum stock is important, and ways you can avoid common mistakes.
Definition of minimum stock levels
Minimum stock levels refer to the minimum amount of stock you allow in your inventory before you need to restock. You do not allow your stock levels to fall below the minimum stock level. It is the opposite of maximum stock levels, which refers to the maximum amount of stock you are able to have in your inventory and on hand.
How to calculate safety stock
Your minimum stock level isn’t a random number you pick out of a hat! You can calculate it using a few metrics that you’ll already have on hand as you run your e-commerce business.
The basic formula for calculating your minimum stock level is Average Daily Demand x Average Time to Sell = Minimum Stock Level (Safety Stock).
An example would be as follows:
You are an eCommerce company selling novelty mugs. Every week you sell an average of 38 mugs through your online marketplace. If we use the formula above, this would be the minimum stock level:
38 divided by 7 = 5.4 (rounded down to 5) = Average Daily Demand
5 x Average Time to Sell (7 days) = 35
35 = Minimum Stock Level
Following this example, you should always have a minimum of 35 mugs in your stock inventory at all times to make sure you can meet demand without any issues.
Why is it important to maintain minimum stock levels?
Keeping a minimum level of stock on hand is vital for stock control. Knowing exactly what's flowing in and out of the warehouse or fulfilment centre and maintaining minimum and maximum stock levels is important for managing customer demand, forecasting and for maximising the amount of warehousing needed to store your inventory. Making sure you have a “safe” amount of stock also allows you to manage any unforeseen problems or react quickly to issues.
If you do not manage your minimum stock levels, you could find yourself struggling with poor inventory performance. You may struggle to meet demand and regularly sell out which impacts your customer service and brand. It could also inflate costs associated with storage, leaving you paying for space you are not utilising.
While selling out of stock is a great sign that your business is thriving, it’s not always great for your customers and supply chain. Keeping a minimum number of stocks always on hand has many benefits.
Benefits of maintaining a minimum safety stock
Cost saving
Optimising costs associated with storage and warehousing is a key benefit of maintaining steady stock levels. By tracking and maintaining minimum stock levels, businesses can avoid overstocking and the associated costs which can impact profits. Maintaining a safety stock also means you’re getting the most out of your storage space.
Avoiding sell outs
While selling out is a great sign that things are going well, regularly selling out is a sign that you do not have your inventory under control. Running out of stock can lead to lost sales and dissatisfied customers. Maintaining minimum stock levels can ensure that they always have product on hand when needed, and the level can be easily adjusted and scaled as the business grows.
Meeting customer demand
Making sure your customers are happy and satisfied is one of the most important parts of running a thriving eCommerce business. Keeping a minimum stock level means that your customers will always be able to rely on you to meet demand. This will improve loyalty and customer retention.
Avoiding supply chain disruptions
Depending on what kind of online business you’re running, sell outs could cause major disruptions in your supply chain. Making sure you have an inventory buffer will help you mitigate the impact of supply chain disruptions, such as delays in delivery or manufacturing.
Minimum stock level strategies
So how do you maintain minimum (and maximum) stock levels? There are plenty of strategies to do so, but it is also possible to simply track what’s going in and out of your inventory with each purchase and shipment by hand or using a spreadsheet — if your business is still in the early stages. However if you’re growing, you might want to implement more automated processes to save time and money.
Track inventory
Keeping track of stock levels is important for several reasons. Inventory tracking allows businesses to predict trends and see what products are most popular so they can adjust inventory levels accordingly. Automated inventory tracking systems can provide real-time information about stock levels, reorder points and lead times.
Set reorder points
Automating reorder points can help replenish stock as soon as it hits the minimum stock level — or in other words, the reorder point. You can set a reorder point by using tools in your inventory management system/ERP integration or work it out using a formula: Reorder Point (ROP) = (Daily Sales Velocity x Lead Time) + Safety Stock.
Identify safety stock
Setting a minimum stock level and reorder point will mean that you always have safety stock on hand if there are any issues, unforeseen events or just a crazy surge in orders. Safety stock can be calculated based on factors such as lead times, sales variability and supplier reliability.
Forecasting
Knowing your minimum stock levels helps businesses predict how well your stock is going to sell in the future, increasing insights into customer demand and sales trends. Forecasting by analysing historical data, seasonal trends, market conditions and customer behaviour can help businesses make smart decisions about their inventory levels. During busy holiday seasons, stock control methods can help you manage your inventory in line with increased demand, leading to more sales and happier customers.
Improve supplier relationships
Maintaining good relationships with suppliers and warehouse management can help your business reduce lead times and ensure timely deliveries. Managing stock effectively can avoid any unhappy conversations with other individuals in your supply chain, and positive relationships can help businesses maintain optimal inventory levels without incurring excess storage costs.
Implement Just-in-Time (JIT) inventory
Alongside minimum stock levels, businesses can implement just-in-time inventory systems which will only order inventory when needed, minimising warehouse holding costs and stopping any excess inventory being built up over time. This kind of system can be an effective way of maintaining optimal stock levels, but you need to have accurate forecasting and efficient suppliers to make it successful.
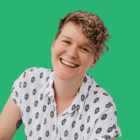
Emily Browne is a writer for ShippyPro who blends her passion for writing with an interest in all things e-commerce. Emily strives to make complex topics more digestible, proving that the world of logistics isn't as confusing as it sometimes feels! Her expertise in supply chain management, coupled with a knack for storytelling, helps readers navigate the complex world of e-commerce and shipping.