The 15 most complex shipping errors and how to avoid them

Shipping errors are far more than a nuisance for day‑to‑day operations: their impact cascades across the entire customer experience, undermining the work of marketing, logistics, customer service—and often even sales.
In this article we outline the 15 most common—and complex—shipping mistakes and provide practical steps to avoid or handle them.
Critical warehouse‑management errors
Warehouse management is the starting point for any efficient shipment. Roughly 50 % of all storage costs are incurred in the order‑picking area, making the picking phase especially prone to mistakes. Although the average error rate is only about 0.3 %, the operational consequences are significant (source).
Wrong picking and look‑alike items shipped
Swapping look‑alike items is one of the most insidious shipping errors. When products share similar size, colour or packaging, the likelihood of confusion rises sharply.
To tackle this effectively, introduce advanced, technology‑assisted picking systems—barcode scanners, pick‑to‑light or pick‑by‑voice—which minimise manual intervention and drastically cut human error.
A well‑defined storage layout should be supported by WMS software that physically or digitally separates similar SKUs and enforces systematic final checks that match barcodes, SKUs and orders before dispatch.
No cross‑check between order and contents
Cross‑checking the order against the actual package contents is a key barrier to shipping errors. If this step is skipped, quantity mistakes and omissions become inevitable. Under pressure, an employee might pack the wrong quantity or miss an item altogether.
Deploy RFID or integrated barcode‑tracking systems within your order and warehouse‑management software. These tools allow systematic controls immediately before cartons are sealed, flagging quantitative or qualitative discrepancies in real time. Back the process with predictive algorithms that detect recurring patterns and anticipate operational issues.
No pre‑shipment quality control
Pre‑shipment QC is the last line of defence against logistics errors. Placed strategically between packing and dispatch, it intercepts defective products before they reach the customer. Around 6 % of shipments are caught for non‑compliance, preventing costly returns and claims.
Statistical controls (Six Sigma, TQM) help spot manufacturing defects, packaging damage or assembly problems. Visual automation using computer‑vision systems greatly increases the speed and accuracy of defect detection.
An integrated approach—controls on receipt and at packing—creates a strong barrier that sharply lowers the risk of shipping faulty goods while ensuring an impeccable customer experience.
Recipient‑data issues
Recipient accuracy directly affects delivery. Statistics show a sizeable share of parcels are undelivered because of incomplete or incorrect address data, causing costly delays and tarnishing brand reputation.
Incomplete address or wrong ZIP/postcode
Postcode errors are especially troublesome because automated sorting relies primarily on the ZIP code. In large cities with multiple postal zones, you must use the specific postcode, not a generic one (e.g. 50134 instead of 50100). An address without a street number invariably leads to a failed delivery.
If a carrier cannot physically access the destination—gated areas, private roads—the delivery will fail as well. To prevent these errors:
- Implement automated address‑validation systems.
- Require active confirmation of the full address before purchase.
- Develop internal protocols to hold or verify orders with incomplete addresses.
Invalid phone number
A phone number, while not mandatory for some carriers, becomes crucial if delivery issues arise. Advanced validation should check:
- No extra spaces before or after the number;
- Compliance with the carrier’s max‑character rule (usually 15);
- Correct country dialling code.
If the courier cannot reach the recipient, the parcel goes into storage, triggering costly return procedures.
Name on intercom doesn’t match order
A mismatch between the order name and the intercom/mailbox label is a frequent, underrated obstacle. Legally, missing names do not justify non‑delivery, yet in practice many attempts fail. Add a “c/o” field in your checkout so customers can specify the name on the intercom—especially vital for business addresses or third‑party locations.
Labelling and paperwork: hidden risks
Incorrect shipping paperwork is the leading cause of delays, with error rates ranging from 6 % to 15 %. Multiplied across high volumes, the operational impact is severe.
Duplicate or unreadable labels
Label legibility is a technical, not cosmetic, issue. Blurry or low‑resolution labels disrupt automated scanning, stopping parcels in sorting hubs. Ensure that you:
- Use non‑reflective white labels;
- Keep text between 8 pt and 12 pt;
- Print high‑resolution files, especially for logos.
Mass printing adds risk if shipping‑software settings are wrong.
Missing or incorrect waybill
The waybill is part of the transport contract (Italian Civil Code, Art. 1684) and serves three purposes: proof, information and receipt.
Each waybill is unique and cannot be reused. For multicolli (multi‑parcel) shipments, you have one waybill stating the exact number of parcels, even though each parcel must show sender and recipient. Keep the document for at least five years for legal and tax reasons.
Using integrated digital platforms to generate electronic waybills (e‑LDV) minimises manual errors, ensures compliance and simplifies long‑term archiving.
Mis‑delivery caused by mixed‑up labels
Re‑using boxes without removing old labels is a prime cause of wrong deliveries. Re‑printed labels stuck on the wrong parcel will be accepted by the system but routed to the wrong recipient.
When using recycled cartons, remove or black out every old barcode or label; automated sorters may otherwise read conflicting information.
Sorting‑center and customs blocks
Sorting hubs and customs offices are the most critical bottlenecks in international shipping. Up to 30 % of cross‑border delays stem from customs or sorting issues.
Parcel rejected at sorting hub
Sorting centers carry out strict compliance checks. Automated systems verify size, weight, shape and label readability. Any irregularity can trigger an immediate reject. Damaged packaging or protruding items are also rejected to protect conveyors and other parcels.
Standardise packaging and run systematic pre‑shipment checks rather than random spot checks.
Incomplete customs paperwork
Customs documentation is the most common stumbling block for non‑EU shipments. You must attach:
- Correctly completed CN23 declaration;
- Commercial invoice (for goods for sale);
- Free Export Declaration (goods value > €1,000);
- Washington Declaration for leather items where applicable.
Ensure all documents carry identical information to the waybill. Even minor discrepancies can hold shipments for days.
Wrong product classification
HS‑code misclassification can result in wrong duties or fines. Vague or incomplete product descriptions likewise delay customs clearance.
Create an internal HS‑code database and run automated checks to ensure description and code match before shipping.
System errors and misconfigured automation
The tech stack is the nervous system of modern logistics. About 30 % of shipping errors stem from IT or badly configured automation, causing delays and unforeseen costs.
Out‑of‑date shipping software
Legacy systems are a critical vulnerability. Skipped updates compromise data security and operational efficiency. Notably, a major credit‑agency breach was traced to a two‑month delay in patching.
- Set automatic updates for all critical apps;
- Schedule them during low‑volume periods;
- Run compatibility tests across interconnected systems first.
Automation that outputs wrong addresses
Poor integration between e‑commerce, warehouse and shipping platforms fragments data, leading to address errors. Real‑time address‑validation APIs that cross‑check against official postal databases should be deployed before labels are generated.
Tracking number not assigned or not communicated
Lack of tracking is a major post‑shipment inefficiency. Causes range from unlabelled parcels to third‑party carriers or external events (road works, weather, strikes) freezing updates for over 48 h.
Develop exception‑management protocols that trigger proactive checks whenever tracking hasn’t updated within predefined limits—before customers complain.
Shipping errors: the bottom line
Shipping is an integral part of the purchase journey—the final link between company and customer. Reducing friction across the logistics chain—from picking and packing to delivery—is therefore essential.
To recap, here are the most common and complex shipping mistakes:
- Wrong picking and look‑alike items shipped
- No cross‑check between order and contents
- No pre‑shipment quality control
- Incomplete address or wrong postcode
- Invalid phone number
- Name on intercom doesn’t match order
- Duplicate or unreadable labels
- Missing or incorrect waybill
- Mis‑delivery caused by mixed‑up labels
- Parcel rejected at sorting hub
- Incomplete customs paperwork
- Wrong product classification
- Out‑of‑date shipping software
- Automation generating wrong addresses
- Tracking number not assigned or not communicated
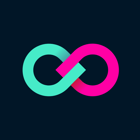
ShippyPro is the complete shipping software for online and offline retail. With Label Creator, Track & Trace, Easy Return and Analytics features, our software simplifies your shipping operations. ShippyPro integrates with over 180 carriers and 80 sales channels, making it compatible with a wide range of products and use cases.