Inbound and outbound logistics: key differences and importance

In today’s dynamic market with rising customer expectations, logistics is indeed the driving force behind smooth operations and happy clients. When we think of logistics, we often picture the final phase of delivering products to the end-consumer, but this is only one piece of a large puzzle.
In fact, the realm of logistics encompasses a vast network of operations, known as inbound and outbound logistics. These connect the dots from when a customer pushes the “Buy Now” button to when an order reaches their doorstep.
Table of contents
- Definition of inbound logistics
- Definition of outbound logistics
- Differences between inbound logistics and outbound logistics
- Integration and Collaboration between Inbound and Outbound Logistics
Definition of inbound logistics
Inbound logistics are all logistics processes related to supply management, namely receiving raw materials, inventory or finished products from the supplier and distributing them to the business’s warehouse, fulfilment centre or retail store.
Definition of outbound logistics
On the other hand, outbound logistics are all logistics processes involving the movement and storage of finished products out of the supply chain, in particular from the business’s premises to the end customers. Processes that qualify as outbound logistics are for example order confirmation, fulfilment, picking, packing, shipping, last-mile delivery and even customer service. Outbound logistics primarily deals with the demand side of the supply chain, ensuring that all products are delivered on time and that customers are satisfied.
Differences between inbound logistics and outbound logistics
The difference between inbound and outbound logistics lies mainly in their purpose, as well as the parties involved in the operations. Inbound logistics aims at securing supplies for businesses, moving inventory, raw materials etc. from the supplier to the business’ premises, whereas outbound logistics focuses on fulfilling orders, meeting customer demand, and moving products from business premises to the end client.
Inbound logistics
Inbound logistics refers to the processes related to managing the supply chain, namely ordering, receiving, storing and organising incoming supplies. Its key components and processes are the following:
1.Supplier relationship management. This activity involves finding reliable suppliers, obtaining price quotes, and fostering relationships.
2.Procurement and purchasing. These activities include negotiating prices, placing orders, and managing contracts. The purpose of efficient procurement practices is to acquire high-quality materials or supplies at competitive prices, ensuring they arrive timely and in the right quantity.
3.Transportation and receiving. These activities involve the movement of goods from the supplier to the business’ premises. For example, this can mean deciding which means of transport to use for the different types of products, contracting with third-party carriers, managing customs compliance, and ensuring that the goods arriving match each order.
4.Inventory management. This includes managing the materials in the warehouse, making sure items are placed in the right locations and conditions, forecasting demand, and maintaining precise records of all materials that enter the warehouse. By efficiently managing inventory levels, businesses can avoid stock outs or overstocks and reduce storage costs.
Challenges and common issues in inbound logistics
Inbound logistics can be a complex aspect of business operations and there are several obstacles that can hinder supply chain efficiency. Let’s examine the most common challenges related to inbound logistics more in detail.
Fluctuating demand and inventory imbalances
Seasonality, consumer trends and economic conditions are only some of the factors that lead to inventory imbalances. Businesses must often deal with sudden changes in demand, where too little stock available means disappointing customers, whereas excess stock ties up capital. The best way to address these problems is to utilise a WMS software to analyse demand patterns based on historical data and make predictions to ensure the right amount of stock is available, thus balancing demand and offer.
Transportation costs
Transportation alone is one of the most expensive aspects of business operations and reducing its costs is a priority for most businesses. Negotiating favourable rates with carriers based on shipping volume or collaborating with shipping partners who have access to better rates is a good strategy to optimise expenses.
Lack of transparency
Not knowing exactly where products are and how much they cost can cause real fulfilment nightmares. Lack of transparency in the supply chain is often cause of inventory problems and delivery delays. Real-time information systems provide visibility into every operation, enabling companies to track shipments and access crucial information for better production planning.
Processing returns
When inventory is not updated promptly due to inadequate returns processing, this can lead to huge problems like inaccurate inventory counts, over or understocking, poor customer experience and wasted resources – just to mention a few. Again, to avoid tripping on your own feet, integrated automation technology can become your real game-changer!
Benefits and significance of efficient inbound logistics
Optimising inbound logistics means having a more efficient supply-chain. This allows for reduced costs and more efficient deliveries to end customers. It is like having a well-oiled engine that propels your business forward. Let’s examine the benefits of efficient inbound logistics more in detail.
Higher customer satisfaction
Less inefficiencies, higher quality of products and faster service mean that your clients will be satisfied with your products and more likely to purchase again, contributing to your growth.
Reduced costs
Efficient inbound logistics reduce costs related to unnecessary storage expenses, improving overall inventory turnover.
Faster deliveries
Thanks to efficient inbound logistics, businesses can deliver orders faster. This aspect is essential to provide a competitive advantage and improve customer loyalty.
Inventory optimization and visibility
With real-time inventory visibility, businesses can track information easily and act promptly in case of errors or need. Moreover, inventory optimization leads to reduced costs and to a balanced supply chain that can respond adequately to changes in demand.
Outbound Logistics
Outbound logistics focuses on product demand, specifically on delivery of products to end customers. It involves order fulfilment, packing, shipping, delivery, and customer service connected to deliveries. Let’s discover its key components and processes more in detail.
- Order processing and fulfilment. It starts from the moment a customer hits the “Buy Now” button on your website until the awaited package timely arrives at their doorstep. However, everything that happens in between is crucial. In fact, once an order is placed, it is sent through the business’s order management system which then transfers the information to the warehouse or fulfilment centre. From here the product must be picked from its location in the warehouse, packed, labelled with the correct details, and prepared for transportation.
- Transportation and distribution. It involves selecting the adequate means of transport (carrier, plane, ship, etc.) for the products, route planning, carrier management, shipment tracking, and ensuring timely delivery. Last-mile delivery, namely delivery to the end customer, is probably the most expensive step for a business but also the most important. Before the last mile, retailers handle lots of orders at the same time in the same way, but here each delivery is unique and tailored to a specific customer with a single address. As you can imagine, it mustn’t go wrong!
- Customer relationship management. Since outbound logistics refers to all processes related to delivering orders to customers, customer support can be considered part of this phase. Handling problems related to order details, fulfilment, or shipping orders promptly is essential to drive revenue and strengthen customer relationships.
Challenges and common issues in outbound logistics
Incorrect or late orders drive customers away and can put a brand’s reputation on the line. The most common challenges outbound logistics must face every day are in fact delivery delays, order errors, lack of communication and inefficient transportation planning.
If you don’t want anybody to doubt your company’s reliability, make sure to understand the root causes of the most common problems to address them proactively, a savvy strategy that is key to stay ahead of competition. And finally, remember to meet the need for speed and provide tracking for trust.
Coordinating operations and transport costs
Monitoring production, storage and distribution while coordinating the movement of goods is a very difficult task. If demand increases, you need to have a flexible logistics partner that can free up more warehouse space and increase its fleet. Also, the high cost of transport is another big issue businesses have to deal with. Partnering with a company that has access to lower shipping rates or investing in software that optimises your delivery routes are effective strategies to reduce expenses.
Inventory costs
Effective inventory management involves finding the right balance between having sufficient supplies to meet customer demand and minimising unnecessary expenses. It is important to constantly monitor metrics such as sell-through rate, inventory turnover, and invest in a WMS software that identifies patterns in demand to optimise your stock levels. Discover the complete list of ecommerce management metrics.
Timely delivery
Delivering products on time is a difficult obstacle to overcome, because it implies having the right items and quantities always available and ensuring that everything is properly packaged. In today’s fast-paced market, customers expect deliveries to happen faster and faster, to be free and trackable. It is therefore necessary to invest in an excellent delivery experience to stay ahead of competition.
Benefits and significance of effective outbound logistics
Effective outbound logistics are directly connected to the success of a business. As mentioned above, even for outbound logistics, technology and automation can be game changers, serving as differentiators for efficiency and reliable partners in achieving significant cost savings.
Cost Savings
Optimising transportation routes and implementing smart route planning thanks to technology can reduce travel times, fuel consumption and travel costs, while resulting in faster delivery.
Increased customer satisfaction
Satisfied customers are more likely to recommend your brand to others and write a positive review on your website. This will improve your brand’s reputation and encourage customers to purchase again.
Less errors
Introducing automation will unlock a new level of efficiency in your outbound logistics processes. In the blink of an eye, you will execute operations like processing orders, generating shipping or customs documents, pick lists, and invoices without potential human error. This not only saves precious time and money but also ensures more accuracy, paving the way for faster order fulfilment and happier customers.
Integration and Collaboration between Inbound and Outbound Logistics
Inbound and outbound logistics encompass many steps that collectively drive the seamless flow of goods throughout the supply chain and have a direct impact on sales. They basically go hand in hand.
Integrating inbound and outbound logistics is essential to coordinate and synchronise activities, reduce delays and improve overall efficiency. When inbound and outbound logistics are integrated, you have greater visibility across the entire supply chain, leading to prompt problem solving and greater flexibility.
Collaboration strategies and tools
Establishing common performance metrics and sharing supply chain objectives, allows inbound and outbound logistics teams to work in the same direction. Also, it is advisable for businesses to coordinate using software systems (e.g., WMS, ERP solutions) to gain better visibility into supply chain operations and be in control of manufacturing, inventory, warehouse management, and monitor customer demand patterns.
Benefits of a synchronised inbound-outbound logistics approach
A synchronised inbound-outbound logistics approach is vital for supply chain management. As mentioned before, these two logistics processes go hand in hand, they rely on each other. When the one falters, the other will feel it, creating a ripple effect through the whole supply chain. This is why a synchronised approach is the key to achieve operational excellence, maximise revenue and increase delivery speed.
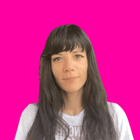
Passionate freelance copywriter, with a niche in ecommerce and logistics. When collaborating with ShippyPro, she loves writing about trends, marketing and communication strategies to help brands gain an edge in an ever-evolving digital landscape.