Logistics value chain: what is it and why it's important

Let’s imagine a company as a machine made of different gears, each representing an activity that contributes to the functioning of the whole system.
A business is, in fact, a sum of interdependent activities, where the goal is not just producing or sourcing goods but finding strategies to add more value to a product, compared to the original cost to source or produce it. This difference leads to what is known as profit margin.
To achieve it, it is essential to analyse the activities that structure the company and understand how they interact to gain competitive advantage. A company obtains competitive differentiation either by performing strategically important activities better than others or by executing them at a more affordable cost.
This is where Michael Porter’s value chain comes into play; it is a model that helps to identify a company’s strategic activities, creating a clear overview of a company’s structure. It is very useful because it sheds light on where value is created and where there is room for improvement. Let’s find out more about it.
What is a value chain?
A value chain consists in the series of activities that businesses undertake to produce their product or service – from acquiring the necessary raw materials, processing them into a finished product, to marketing and distribution.
The concept of value chain was first introduced by US economist Michael Porter in 1985, with the objective of identifying activities that are strategically relevant to a company, enabling them to gain a competitive advantage.
He wrote: "Competitive advantage cannot be understood by looking at a firm as a whole. It stems from the many discrete activities a firm performs in designing, producing, marketing, delivering, and supporting its product."
In his famous book The Competitive Advantage, Porter identifies five primary activities of the value chain:
- Inbound logistics: activities involved in receiving, storing, and organizing raw materials or inputs a company uses to produce its goods or services.
- Operations: the processes related to transforming the materials into finished products.
- Outbound logistics: activities involved in distributing the products - like shipping, transport management, as well as delivery to end customers.
- Marketing and sales: activities related to promoting the products and acquiring potential customers.
- Service: activities related to enhancing customer experience - like providing post-purchase support or managing returns.
Support activities
According to Porter there are also a series of support activities that enhance the value of the final product and benefit the primary activities. These include:
- Procurement refers to how a business obtains raw materials, supplies, as well as assets such as machinery, laboratory equipment or office equipment. Procurement is essential in the support of all value chain activities, not just those related to inbound logistics.
- Technological development enhances processes and helps to meet customer needs more effectively - like implementing automation software, product design research and other technological innovations.
- Human resources (HR) management involves recruiting, hiring, and managing personnel. Efficient HR management contributes to the business’ competitiveness, since ensuring employees with the right skills work in the right positions is central to achieve business objectives.
- Infrastructure activities like planning, accounting, finance, legal and quality control. Often smaller decisions are based on these activities. In fact, defining the right strategies is essential to ensure smooth and effective operations across all departments.
It is important to understand that the value chain is not a sum of independent activities. One must imagine it as a system of interconnected and interdependent processes. For example, a decision made in procurement can impact product quality and outbound operations. In the same way, improving one department can bring benefits to others. For instance, implementing automation software (technology development) can improve order fulfillment (outbound logistics) and customer satisfaction or investing in employee training can lead to better customer service and assistance.
What is the difference between supply chain and value chain?
While both supply chain and value chain are interconnected and serve the common goal of creating a robust, profitable company, they differ in their processes.
A supply chain is mostly physical, and its focus lies in logistics, namely from building the product (e.g., procuring raw materials) to delivery to the end customer.
A value chain can be defined as the lens through which a company looks into these processes to create customer value. In other words, the value chain encompasses the supply chain, but uses it as a tool to understand what customers want and to enhance customer experience.
Importance of the logistics value chain
Logistics plays a key role in Porter's value chain model; effectively managing inbound and outbound logistics maintains a steady supply of raw materials for production, efficient inventory management, and agile distribution to customers.
Indeed, a mistake in any step of either inbound or outbound logistics can lead to service disruptions and, ultimately, negatively impact customer satisfaction. For example, procuring low-quality materials or delivering to the wrong addresses are synonymous with poor service and additional costs to the company.
On the other hand, a well-developed logistics infrastructure lays the foundation of a thriving business and becomes an asset for competitiveness. Firstly, efficiently handling logistics through automation technology can bring significant cost savings which a company can transfer to its customers, either by offering better pricing or by developing more products. Secondly, when orders are processed quickly and delivered swiftly, customers are satisfied and therefore more likely to become repeat buyers.
How to perform a logistics value chain analysis
A logistics value chain analysis is essential to pinpoint areas where costs are too high or where you can create a competitive edge, including warehousing, order picking, and goods distribution. To perform a thorough analysis of your logistics value chain, follow these three steps:
- Categorise activities in your inbound and outbound logistics operations by identifying internal processes and strategies. In this way, you can better understand how operations work and the allocated resources.
- Analyse value and costs. Identify direct and indirect costs and which activities provide a competitive edge.
- Define a strategy. Ask yourself the question: how can I increase the value of what I offer? The objective of this strategy is to understand how to offer something that is better, by optimising resources and increasing profitability. Additional value can be obtained by investing in new technology, personnel or by reorganising logistics operations.
Digitalisation: a game-changer for the logistics value chain
Porter himself found that technology has been a game-changer in the value chain, boosting companies in their activities and productivity levels. Compared to manual data entry, automation and technology are far more powerful, allowing to record and analyse vast amounts of new data across all activities. Moreover, technology streamlines the flow of information across the different areas of a business, improving management and decision-making processes.
An increasing number of companies are also implementing WMS Systems to constantly keep track of activities within the logistics value chain. In this way, they have more information available compared to manual management, leading to better decision making and more effective strategic planning.
How to improve the logistics value chain
Inbound logistics value chain analysis
Inbound logistics comprises the procurement, storage, and management of resources with the objective of ensuring that the right materials arrive at the right time in optimal condition. Using value chain thinking in this department means, for example, implementing Just-in-Time inventory to minimise waste and costs. Other ideas can be implementing software to speed up certain processes, improving quality control or creating personalised versions of a certain product.
Outbound Logistics value chain analysis
Outbound logistics comprises activities like storage and distribution of products. Using value chain thinking in this department can mean, for example, integrating technology that sends customers real time tracking and delivery notifications, updating them on the journey of their orders. Such transparency will benefit both the business - by increasing operational efficiency - and customers - by enhancing their experience. Another example of value chain thinking can be integrating with Multiple Carriers, offering users a wider range of shipping options, and allowing them to choose the most cost-effective solution for their needs.
Conclusion
Competitive advantage cannot be achieved by looking at a company as a whole, but rather by observing the multitude of interconnected activities that contribute to its functioning. This approach helps to identify areas of improvement more effectively or plan strategies to add more value.
Optimising the logistics value chain is crucial for building a robust business.
In this sense, digitalization has revolutionised the logistics value chain, enhancing flexibility, productivity, and communication across the different departments of a business, thereby contributing to its optimal functioning. As companies increasingly leverage automation technologies and embrace innovative solutions, they are better positioned to drive competitiveness and deliver value to their customers.
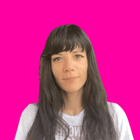
Passionate freelance copywriter, with a niche in ecommerce and logistics. When collaborating with ShippyPro, she loves writing about trends, marketing and communication strategies to help brands gain an edge in an ever-evolving digital landscape.