Multi-store logistics: navigating shipping and expansion

Shipping and logistics plays a pivotal role in any online business as it expands, but with expansion comes more complexity in inventory management, warehousing and reverse logistics. While this is a great problem to have, it’s still a hurdle that growing businesses need to navigate.
There is a lot of potential in multi-store expansion, but it involves reworking your logistics processes to accommodate the new locations and inventory. This article aims to break down everything you need to know about multi-store logistics so you can streamline operations as you grow your business.
The logistics of multi-store expansion
Taking your business to the next level can be a daunting process — especially if you need to rethink your logistics processes to accommodate it. Operating multiple stores at once requires coordination and careful planning to meet customer expectations. One way to do this is through multi-store logistics, sometimes called multi-store fulfilment or multi-store warehousing.
Multi-store logistics is a supply chain and logistics strategy used by retailers and e-commerce businesses to optimise the distribution and fulfilment of products in multiple store locations. The approach works best for businesses that have both physical stores and an online presence. Multi-store logistics can help stay on top of fast-paced fulfilment processes, streamline operations, reduce overall shipping costs and improve the overall customer experience. There are a lot more complexities to consider when it comes to managing multiple stores, warehouses and locations. While it is a good sign that your business is thriving, it also involves a new strategy to meet customer expectations.
The importance of a centralised vs. decentralised distribution strategy
How you plan and execute your logistics strategy will depend on whether you want a centralised or decentralised approach. But what’s the difference?
- In a centralised system there is a single central hub for all logistics operations. This traditionally looks like a single warehouse that controls inventory and the flow of all goods. Large enterprises will have multiple hubs serving different geographic regions, but still control all warehousing and logistics processes.
- A decentralised system leverages multiple strategic locations to store and deliver inventory closer to the end customer. These locations, called ‘nodes,’ are often placed close to key transportation routes or urban areas.
When it comes to multi-store logistics and expansion, both a centralised and decentralised approach have their pros and cons. A centralised approach tends to be more cost effective and helps vendors have more control over their inventory, shipping and all aspects of the supply chain. However a decentralised approach can help vendors process a larger volume of orders to a widely distributed customer base. Which one you go for will impact how you navigate shipping as you expand.
What are the challenges shipping for multi-store operations?
There are a number of challenges when it comes to multi-store logistics which need to be considered before expanding into a new region.
Managing inventory across various locations
One of the biggest problems businesses encounter is how to manage inventory across multiple geographic locations. Keeping track of the flow of goods and discrepancies between what is shown as available online and what is actually in stock can lead to customer dissatisfaction and order fulfilment issues.
Ensuring timely deliveries and consistent stock levels
Ensuring accurate and real-time inventory visibility across all your locations can be challenging. Having multiple stock outs or differing stock levels in different warehouses can lead to delivery issues or delays as you need to control stock more effectively.
Addressing regional variations in shipping regulations and requirements
As you expand into new regions you’ll encounter differences in shipping regulations and requirements. It’s important that online businesses enact due diligence in this regard to avoid occurring fines or other issues that could hinder business expansion.
4 Strategies for multi-store logistics
With this in mind, how can e-commerce stores tackle these challenges? Thankfully, modern technology has stepped in to help in a number of ways, as well as traditional methods like improving relationships with suppliers.
Utilising modern Inventory Management Systems (IMS)
Modern inventory systems track products all along the supply chain. It automates core logistics processes related to tracking stock from when they arrive in a warehouse (or other hub) to the moment they leave it. This is done by combining varying software packages to track stock levels and movements.
There are various different types of IMS systems, including warehouse inventory management systems (WIMS), manufacturing inventory management system (MIMS) and retail inventory management system (RIMS).
Reliable logistics partners
Having strong relationships with reliable business partners is key to a multi-store logistics strategy. Online stores should partner with 3PL services or warehouses that are able to meet and fulfil their business goals, which includes scaling and expansion. By leveraging reliable, long term logistics partners, businesses can access a network of hubs and nodes that will help them distribute in new regions.
Considering a hub-and-spoke distribution model
Another way to improve logistics while expanding operations is to employ a hub-and-spoke distribution model. This strategy is named as such as it resembles the wheel of a bicycle, with a large central “hub” connected to “spokes” that are connected to the hub. This analogy describes how a business will run operations out of a single large hub which is then connected to a number of organised shipping routes. This strategy allows the vendor to have complete control over the flow of goods and supply chain from a single location, adding “spokes” as it expands.
Leveraging technology for seamless operations
Ultimately, multi-store logistics strategy is made so much easier through technology. IMS systems help you track inventory levels and the flow of goods from A to B using a single interface. Tech tools can aid in real-time inventory tracking in a number of ways. Barcodes and RFID (Radio-Frequency Identification) tags and readers monitor stock in real time as it moves along the supply chain. Mobile devices equipped with inventory management apps then enable staff to update inventory information in real time.
Cloud-based inventory management systems further allow businesses to access real-time inventory data from anywhere with an internet connection. This flexibility is particularly useful for organisations with multiple locations and warehouses.
The benefits of integrated logistics platforms
By integrating IMS systems into point-of-sale and e-commerce platforms, online stores can ensure inventory levels are automatically updated as sales are made. This is one of the benefits of a fully integrated logistics platform, as this real-time synchronisation helps prevent overstock or stockout situations no matter where the stock is located. They also offer end-to-end visibility of the entire supply chain. This visibility helps in making informed decisions and quickly responding to any issues or delays.
Integrated logistics platforms support efficient, accurate fulfilment, allowing businesses to quickly allocate inventory, route orders and optimise delivery routes. Furthermore, these platforms help save money through reduced transportation costs, labour and overhead expenses.
Embracing automation and AI for forecasting and distribution
AI is everywhere these days — even in the logistics industry. Advanced technologies like machine learning and artificial intelligence (AI) can be used for demand forecasting and predictive inventory management. These tools analyse historical data and real-time information to make proactive decisions about inventory levels. AI can also inform businesses on how to adjust pricing based on real-time supply and demand data to optimise profitability.
AI can help inform business owners on where and how to automate inventory management and order fulfilment to reduce manual tasks. Many processes in multi-store logistics can be automated, especially when IMS systems are in place to monitor inventory levels and supply chain in a number of locations. Other management systems can also automate order routing by intelligently allocating orders to the most suitable fulfilment centres based on inventory availability, proximity to the customer, and other factors.
While scaling an online business can come with challenges, the amount of technology available to vendors can help make processes far more manageable no matter the size of your business and where in the world you want to serve.
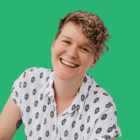
Emily Browne is a writer for ShippyPro who blends her passion for writing with an interest in all things e-commerce. Emily strives to make complex topics more digestible, proving that the world of logistics isn't as confusing as it sometimes feels! Her expertise in supply chain management, coupled with a knack for storytelling, helps readers navigate the complex world of e-commerce and shipping.