A guide to warehouse automation (2025)

For modern distribution companies, automated processes are an important way to modernise and increase efficiency. Warehouse automation systems are installed to replace tedious labour intensive activities with the goal of streamlining operations.
More than 80% of warehouses worldwide have no automated systems installed whatsoever, which gives the warehouses that do have an edge over the competition. Furthermore, the need for warehouse space in the UK has grown greatly so it's a good time to invest in automation to meet demand. In this article we will explore everything you need to know about warehouse automation and how it can benefit your supply chain.
What is warehouse automation?
Warehouse automation refers to the process replacing repetitive, time-consuming or labour intensive warehouse activities with automated technology. Each warehouse will implement their automated processes differently, and it depends on where the businesses sticking points are and what they want to improve. Many tasks within a warehouse can be automated, including:
- Picking
- Packaging
- Receiving
- Sorting
- Returns
- Inventory management
- Shipping
- …and many more!
Many processes within a warehouse can be replaced by automated systems. Warehouse automation reduces human error, increases efficiency and can reduce costs, which makes it a popular investment for warehouse managers wanting to modernise their activities and remain competitive.
Why should you replace processes with warehouse automation?
There are many reasons why warehouse managers and businesses might want to replace their processes with software or robots. Common reasons for doing so include optimising operations that need too many people or take too much time, repeated problems with order fulfilment, difficulty staying on top of inventory and errors in picking, packaging and shipping. It’s in the warehouse's interest to make sure that they run an effective, efficient service so it’s vital that any issues that affect customer satisfaction can be met with solutions such as automated systems. Warehouse automation is important when creating a warehouse picking strategy.
Benefits of warehouse automation
Warehouse automation provides warehouses with a long list of benefits. While you can’t replace absolutely every process with a robot or software, there are many reasons to optimise where possible. Benefits include:
Increased efficiency
Automated systems reduce time spent manually picking products, travelling between different areas of the warehouse and increases productivity and shipping flow by making the work simpler and easy to manage.
Reduced human error
Automated systems such as software and AI-powered robots reduce the amount of errors which could be caused by warehouse workers. It also allows for more accurate inventory management by leveraging technology to automatically count items.
Reduced operational costs
While implementing warehouse automation can be expensive and complex, it has an impressively fast ROI which helps warehouses save money in the long run. By running automated systems, the need for new staff and training is reduced, human errors are minimised and there is less risk of product loss and damage which can all affect a warehouse's bottom line.
Competitive edge
These days it is vital for warehouses to remain on the cutting edge if they want to attract more businesses to use their services. Warehouses who do not leverage technology might find themselves struggling to compete with those that have upgraded.
Improved inventory visibility
Warehouse automation improves the accuracy of data collection, allowing for increased visibility into how inventory passes in and out of the warehouse as well as allows easier access to real-time stock data which will improve customer service.
Maximises space
Automated systems can help warehouses maximise their space. An example of this is that robots generally require less space than people, so aisles can be made narrower and don’t need to adhere to safety standards.
Long-term sustainability
Sustainability is fast becoming a key USP for many industries including e-commerce. Effectively automating warehouse processes increases sustainability by using less energy, which in turn will reduce waste and lower the environmental impact of the facility.
Challenges with warehouse automation
The main issue with warehouse automation is that it can be very expensive to implement new and difficult to upgrade or adapt once it’s part of the warehouse's processing strategy. The upfront costs of automated systems is high, but the average ROI is approximately 10 years.
Highly automated warehouses are not as flexible as manual warehouses which rely on workers to perform tasks. When thinking about warehouse automation it’s important to take scalability into account, and to make sure that the solutions you choose can be integrated alongside the tools and software you already have in the warehouse. Another factor to keep in mind is service and maintenance costs.
Types of warehouse automation
As listed above, there are many jobs within a warehouse that can be replaced by automated systems. Here are just a few of the most common ways warehouses will modernise their processes:
Goods-to-person (GTP) solutions
Goods-to-person (GTP) solutions include robots or machines that combine automated storage with accurate picking processes. GTP solutions eliminate walking time and reduce the number of inaccuracies which can be caused by human error. Product data is stored within a system so that the operator knows which items to pick. Once the products have been selected, technologies such as AI-powered robots (see below) or conveyor systems are able to find and move the product into the next phases of the delivery process. GPT helps eliminate errors that can often be a challenge in high-speed or high-demand warehouse environments.
Handheld terminals (HHT)
Handheld terminals (HHT) can be thought of as a warehouse-specific smartphone. They are data processing handheld terminals which warehouse workers can use to quickly find products to prepare for picking and processing. Lightweight and intelligent, handheld terminals are easy to implement and are excellent for real-time data collection and processing functions.
Pick-to-light systems
A pick-to-light system is a simple but effective warehouse automation tool which uses LED lights and barcodes to find products for order fulfilment. The operator will scan a barcode which will then illuminate a path to guide the operator to the right storage location. Once the correct package has been selected, the operator can confirm the picking and move it to the next step in the shipping process. Automated systems also help with other types of picking, including batch picking and wave picking.
Automatic Guided Vehicles (AGVs) & Autonomous Mobile Robots (AMRs)
Automatic Guided Vehicles (also known as AGVs) are portable vehicles which use wires, radio waves, magnets, lasers or vision cameras to navigate around the warehouse. They are mostly used to transport heavy goods or tow products between locations. AGVs come in a variety of models and can be used to move products along an assembly line, transport goods throughout the warehouse and deliver products from one area to another.
Autonomous Mobile Robots (AMRs) also work collaboratively with warehouse staff to complete orders and send them off for shipping. They rely on advanced sensors, AI software and a digital layout which allows them to interpret their surroundings. They will usually be integrated with the warehouse control system and warehouse management system which allows them to follow optimal routes and mean less walking time for workers.
Warehouse management systems (WMS)
As well as all the intelligent robots, vehicles and scanners available to enhance warehouse processes, implementing the right software for the warehouse's business goals is also important. Warehouse management systems are key to developing a competitive edge by minimising labour costs and improving customer services. When it comes to third-party logistics businesses (3PL) which leverage warehouses to pick, pack and deliver goods, the three types of WMS are Standalone Warehouse Management, Supply Chain Execution Modules and Integrated ERP. Which one you choose depends on function, warehouse size, cost and customer needs.
These days successful warehouses need to leverage technology — however the process of doing so is no small undertaking. That said, implementing and upgrading warehouse automation is important for optimising e-commerce processes, keeping competitive and running a more efficient work environment. In the long run, automation will only improve the day-to-day running of the warehouse and keep your customers continually using your service.
Warehouse Automation FAQ
What processes can be automated in the warehouse?
Automation can be used for many of the activities and processes in a warehouse, including sorting, inventory, picking, moving, packaging and receiving. Warehouse automation like robots, conveyor belts and data collection software all help optimise day-to-day warehouse processes.
Will warehouses be fully automated?
It is unlikely that warehouses will become 100% fully operated. Warehouses still need a human workforce to run their automated systems.
Will warehouse automation replace jobs?
While this might be a concern, warehouse automation is very unlikely to completely replace a human workforce. Warehouses still require humans to run their systems effectively, manage customer feedback and monitor processes. In fact, most warehouse workers want better technology to assist them. What automation offers is better use of their time, while leaving all the repetitive picking, packaging, relocating, sorting and shipping tasks to the machines.
What are the three levels of warehouse automation?
The three levels of warehouse automation are Informed, Manual and Fully Automated.
- Informed: These are computer-driven systems which depend entirely on humans to run. Informed systems require human input to make routine decisions and support teams. These include automated systems such as handheld devices and scanners.
- Manual: A manual system is one which uses workers to perform all activities in a warehouse.
- Fully automated: On the opposite end, fully automated warehouses leverage extensive conveyors, sorting equipment, automated storage and retrieval systems (AS/RS).
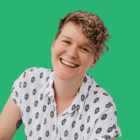
Emily Browne is a writer for ShippyPro who blends her passion for writing with an interest in all things e-commerce. Emily strives to make complex topics more digestible, proving that the world of logistics isn't as confusing as it sometimes feels! Her expertise in supply chain management, coupled with a knack for storytelling, helps readers navigate the complex world of e-commerce and shipping.