AI-powered shipping optimisation to speed up order fulfilment

By now you’ve likely pushed your route-planning spreadsheets to their limits: the UK logistics sector is under unprecedented pressure to deliver faster, greener, and more reliable services.
E-commerce volumes have surged by nearly 25% year-on-year, while consumer expectations for narrow delivery windows continue to tighten. Traditional optimisation methods—manual route planning, spreadsheet-based load building, siloed forecasting—no longer suffice.
AI-powered shipping optimisation represents the next frontier: seamlessly integrating real-time data, advanced algorithms, and automated decision-making to drive step-change improvements in cost, service and sustainability. This guide delves deep into the technical foundations, practical workflows and strategic considerations necessary for medium-to-large UK logistics operations to harness AI effectively.
Modern lakehouse architectures unify real-time telematics and TMS/WMS data for scalable model training and sub-second inference. Hybrid optimisation engines pair MILP solvers with heuristic refinements for dynamic routing alongside predictive demand planning and anomaly detection.
Operational workflows feature micro-adjustments via driver apps, AI-driven exception recovery, intelligent load balancing and proactive customer communications. A phased implementation roadmap covers pilot selection, data foundation, integration, scaling and continuous retraining. Track key KPIs—cost per parcel, on-time rate, carbon intensity—and consult FAQs on TMS integration, digital twins and ROI timelines.
What is AI-powered shipping optimisation?
At its core, AI-powered shipping optimisation uses machine learning and advanced analytics to automate and enhance every stage of the shipping process: from route selection and load consolidation to exception management and performance forecasting. Unlike rule-based systems, AI models learn from historical and real-time data streams (GPS, sensor telematics, weather, traffic) to predict delivery outcomes, dynamically adjust plans, and continuously improve over time. Key differentiators include:
- Closed-loop feedback: Models refine predictions based on actual performance, reducing forecast error over successive delivery cycles.
- Multi-objective balancing: Algorithms can optimise concurrently for cost, carbon emissions, service level, and asset utilisation.
- Scalability & resilience: Cloud-native or edge-enabled inference ensures decisions remain robust under data spikes and network outages.
For a logistics manager with decades of operational expertise, AI transitions optimisation from “what-ifs” in Excel to data-driven, automated orchestration delivering measurable ROI and elevating strategic value.
Architecture & data to power AI-driven logistics
A resilient AI shipping platform hinges on a modern data architecture that ingests, processes and stores vast volumes of heterogenous data.
Data ingestion and integration
A modern shipping platform must draw on both real-time feeds and business transactions.
Vehicle telematics—GPS positions, engine health, temperature sensors—are streamed at regular intervals into a central hub, where they join order and inventory events from your TMS/WMS.
By using resilient, managed pipelines (e.g. cloud streaming services), you ensure that a sudden traffic delay or refrigeration alert becomes immediately visible to optimisation models and planners alike. This unified view of operational and transactional data lets you react faster without manual hand-offs.
Storage and processing
Once data arrives, it’s organised in a hybrid “lakehouse” architecture: a scalable object store for raw, historical records, paired with a query layer optimised for analytics dashboards and model training.
Overnight batch jobs refresh machine-learning features—such as average traffic delays or typical customer-window adherence—while a lightweight real-time service serves updated route suggestions to driver apps with sub-second latency. This separation of heavy-duty training and low-latency inference keeps both nightly retraining and on-the-fly planning running smoothly.
Data quality and governance
High-impact AI depends on clean, consistent data. Implementing a single source of truth for key entities—vehicles, depots, drivers—prevents duplicate or conflicting records from creeping into your models.
Automated checks flag missing or out-of-range sensor values, and versioned feature stores let you track exactly which data fed each model iteration. Meanwhile, encryption and role-based access ensure any personally identifiable information stays GDPR-compliant, and audit logs maintain full transparency for regulators or internal reviews.
AI algorithms for shipping optimisation & applications
Route optimisation
Effective routing combines mathematical rigour with real-world flexibility.
A core optimisation engine solves the bulk of assignments—matching orders to vehicles while respecting delivery windows and driver hours—then a heuristic layer refines those routes by testing minor adjustments against live traffic and weather feeds. This two-stage approach delivers near-optimal plans in seconds, while still allowing urgent manual overrides when exceptions occur.
Read more about route optimisation.
Demand forecasting & anomaly detection
To stay ahead of peaks and dips, we layer statistical forecasting (such as moving-average and seasonal models) with lightweight machine-learning predictors trained on past shipment volumes, promotions or public holidays.
When actual volumes deviate significantly—say a sudden regional disruption—automated anomaly detectors alert planners to investigate before SLAs slip. This combination of forecast and exception monitoring helps you balance capacity weeks in advance and mitigate surprises in real time.
Read more on Demand Planning.
Load planning & capacity matching
Optimising load builds isn’t just about filling every cubic metre. The ideal approach assigns each incoming order a score based on weight, volume and carbon impact, then uses a network-flow algorithm to consolidate shipments into vehicle or container bookings. This ensures high utilisation without breaching weight limits or hazardous-goods rules, and can even suggest re-routing smaller parcels to alternative carriers when it preserves margin or reduces emissions.
Simulation & scenario testing
Rather than roll out changes blind, you can validate strategies through digital-twin simulations of your network.
A lightweight model of depots, vehicles and typical demand patterns lets you run “what-if” scenarios—introducing an unexpected strike at a key port, for example—to see how buffer times, staffing or vehicle allocations should adjust. By stress-testing plans against dozens of hypothetical disruptions, you build resilience without disrupting live operations.
Operational workflows for shipping optimisation with AI: 4 examples
Dynamic route execution
In practice, AI-enhanced routing begins with a batch-generated plan assembled 12–24 hours ahead of departure, incorporating predicted traffic patterns, customer time-windows and vehicle capacities. Once the plan is live, a lightweight inference service ingests real-time telematics and external feeds (traffic, weather, port status) to issue micro-adjustments.
These updates—delivered via mobile-optimised driver apps or in-cab terminals—can re-sequence drop-off orders, swap parcels between vehicles or even trigger mid-tour transfer points when delays exceed predefined thresholds. By embedding AI decisions directly into execution, planners shift from constant manual re-routing to overseeing exceptions flagged for human intervention.
Exception management & recovery
No system is immune to disruptions: adverse weather, customs holdups or hub congestions will occur. Advanced exception-management workflows leverage AI to categorise incidents (e.g., customs delay vs. mechanical fault) and recommend recovery actions. For instance, if a refrigerated trailer’s temperature rises above threshold, the system can automatically reassign temperature-sensitive loads to a nearby vehicle with capacity, notify maintenance crews and alert affected customers—all within minutes.
This proactive orchestration reduces reliance on call-centre triage, preserves service levels and sharply cuts average resolution times.
Intelligent load balancing
Traditional load planning often leaves unused capacity or forces costly last-minute carrier swaps.
Modern platforms assign each incoming order a composite score—factoring weight, volume, promised service level and carbon footprint—and solve a time-sliced network-flow problem to maximise utilisation across owned and contracted fleets. When spot-rates on third-party carriers dip below a threshold, the system can automatically shift marginal loads away from owned assets, optimising cost and sustainability without manual negotiation.
Customer communications
Predictive ETAs and narrow delivery windows are only valuable if communicated effectively.
AI platforms generate dynamic delivery slots based on probabilistic models of route adherence, then present these options to customers via SMS, email or embedded web trackers. Should a delay occur, automated notifications explain the cause (“route recalculated due to accident on M25”) and propose revised windows or self-service rescheduling links. This level of transparency reduces inbound customer enquiries by up to 30% and lifts satisfaction scores, as customers appreciate both precision and context.
Implementation roadmap for AI shipping
Phase 1: process mapping & pilot selection
Begin by mapping end-to-end shipping workflows, identifying high-impact areas—route planning, load consolidation or exception handling. Select a controlled pilot scope (e.g., a regional fleet segment) and define baseline KPIs such as cost per delivery, on-time rates and CO₂ per parcel.
Phase 2: data foundation & model development
Establish data pipelines for telematics, TMS/WMS events and external feeds. Deploy a lightweight feature store to capture essential predictors—traffic delays, historical transit times, load factors—and build initial ML models for routing or forecasting. Validate accuracy and performance against pilot data.
Phase 3: integration & scaling
Containerise inference services and embed them into TMS/WMS interfaces via REST or gRPC. Roll out driver-app integrations for live route updates and dynamic load plans. Expand models to cover additional geographies, vehicle types and service tiers, conducting A/B tests to measure uplift.
Phase 4: adoption & continuous improvement
Implement change-management programs—training sessions for planners, real-time dashboards for operations leads and regular post-mortems on exceptions. Automate nightly retraining cycles and incorporate new data sources (e.g., customer feedback, maintenance logs) to refine models continuously.
Challenges & best practices to integrate AI into shipping workflows seemlessly
Bridging legacy & future systems
Legacy TMS and ERP platforms may lack native APIs or struggle with high-frequency event loads. Mitigate this by introducing a middleware layer—Kafka, Debezium or purpose-built connectors—that decouples core transactions from AI services, enabling independent scaling and versioning.
Ensuring model transparency
Logistics planners must trust AI recommendations. Integrate explainability tools (SHAP, LIME) into decision dashboards to surface the key variables driving route choices or load allocations. Transparent insights foster user buy-in and streamline exception reviews.
Driving organisational change
AI is as much about people as technology. Establish cross-functional “AI champions” in planning, dispatch and customer service teams to evangelise new workflows. Celebrate quick wins—fuel savings, SLA improvements—to build momentum and secure broader executive support.
Define success metrics and KPIs
Deploy real-time operations dashboards for planners and executive-level scorecards updated weekly. Implement automated alerts for KPI deviations—e.g., when on-time rates fall below thresholds—enabling rapid root-cause analysis and corrective action.
- Track a holistic set of indicators, including:
- Cost per Unit (fuel, labour, processing)
- On-Time Delivery Rate (target ≥98%)
- Carbon Intensity (kg CO₂ per parcel)
- Asset Utilisation (empty-running percentage)
- Customer Experience (NPS, enquiry reduction)
ShippyPro’s Zero-Click AI-powered shipping automation
ShippyPro AI tools eliminate manual work from your daily operations. Set once, scale forever.
From courier selection to label generation, automation rules do the heavy lifting — so you don’t have to.
Hands-free fulfilment flow
From the moment an order is placed, ShippyPro’s AI handles courier selection, label creation and document generation without any manual clicks. That “set-and-forget” approach delivers up to +60% faster end-to-end shipping operations and 50% less time spent on order preparation, freeing up 7,000 hours per year from routine tasks.
Prescriptive insights on demand
Rather than just reporting what went wrong, ShippyPro surfaces weekly trend reports on cost spikes, delivery delays and orders in exception. You get clear guidance on what to fix next—letting your team focus on continuous improvement instead of chasing down issues.
Conclusion
AI-powered shipping optimisation offers UK logistics managers a clear pathway to double-digit cost reductions, elevated service standards and ambitious sustainability targets.
By following a phased roadmap—anchored in robust data foundations, guided pilot deployments and rigorous change management—organisations can unlock measurable ROI within months. The time to embrace AI is now: assemble your cross-functional team, partner with proven technology providers and begin transforming your shipping operations into a strategic competitive advantage.
More on AI and logistics
AI-powered shipping optimisation: FAQs
How do I integrate an AI optimiser into my existing TMS?
Leverage middleware connectors or APIs to stream manifest data to the optimisation engine and receive updated route plans. Many TMS platforms (SAP TM, Oracle Logistics) support REST/gRPC extensions for seamless coupling.
What data do I need for a digital twin?
At minimum, geo-tagged assets (vehicles, hubs), historical telemetry logs (routes, speeds, delays) and environmental inputs (traffic, weather). Higher-fidelity twins ingest IoT sensor streams for temperature, load integrity and real-time status.
How soon will I see ROI from AI shipping optimisation?
Pilot programmes typically yield measurable gains—5–10% fuel savings and improved service—in 3–6 months. Full-scale roll-outs can achieve first-year ROIs of 150–300%, combining cost, asset and sustainability benefits.
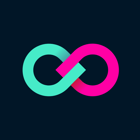
ShippyPro is the complete shipping software for online and offline retail. With Label Creator, Track & Trace, Easy Return and Analytics features, our software simplifies your shipping operations. ShippyPro integrates with over 180 carriers and 80 sales channels, making it compatible with a wide range of products and use cases.