End-to-End Logistics: streamlining the supply chain journey

When it comes to e-commerce, how you run your supply chain will become an incredibly valuable part of your business no matter how big or small your operation is. This process, which includes procurement, distribution, warehousing and delivery, is called end-to-end logistics.
In this article we will break down why an integrated, streamlined and holistic approach to end-to-end logistics can improve efficiency, enhance visibility and increase customer satisfaction.
What are end-to-end logistics?
End-to-end logistics (sometimes referred to as E2E) is the term that encompasses all the processes that businesses may need to engage with to successfully run their supply chains. Processes can vary depending on the specific industry and supply chain, but the majority tend to include:
- Demand forecasting
- Inventory planning and management
- Supplier selection and evaluation
- Order fulfilment
- Invoicing
- Inventory storage
- Order picking and packing
- Shipping and transportation
- Carrier selection
- Shipment tracking
- Logistics information systems (WMS, ERP, etc)
- Risk management
- Performance Measurement and KPIs
- Reverse logistics
- Customer service
- Packing and labelling
- Environmental/green logistics practices
All these various processes work together to make sure that products are sourced, produced and delivered efficiently to meet customer demands while minimising costs and optimising the overall supply chain. Making sure all these moving parts work together effectively and holistically is a key part of successful supply chain management.
End-to-end logistics: a complete overview
In e-commerce, end-to-end logistics is how businesses get orders from the warehouse to the customer’s front door. It covers all areas of the supply chain. Successful end-to-end logistics should integrate transportation, warehousing, distribution, and more into a smooth and efficient operation. Here is what that looks like:
1. Online store and order processing
For online stores, end-to-end logistics processes begin with an online store and order processing. Items will be listed for sale on an e-commerce platform, such as Shopify or PrestaShop. When the customer places an order and processes the payment, they will receive confirmation of their purchase.
2. Inventory management
The purchase will trigger the next step in the supply chain. Warehouses and e-commerce stores should implement real-time tracking of product availability on their websites so customers aren’t disappointed, and integrate this with order processing systems to keep the website up-to-date — especially in busy periods. Knowing when to restock can help businesses avoid stock outs or spending too much money on storage.
3. Warehouse management & order fulfilment
A warehouse, 3PL service or fulfilment centre will store and organise inventory on behalf of the vendor. When an order comes through, a warehouse management system (WMS) will find the order and process it for delivery. This involves packaging the item and labelling it, which takes us into the next step of the end-to-end logistics process: order fulfilment. Packaging should be secure and cost effective.
4. Shipping and transportation
Most large warehouses will have a number of carriers integrated into their logistics processes, but some don’t so e-commerce stores may have to narrow down the right carrier for them based on cost, speed, size and reliability. Shipment tracking and real-time updates are now non-negotiable — customers should receive regular updates on their orders location and time of delivery.
5. Last-mile delivery
Last-mile delivery is just that: the last mile. Local courier services can be mobilised to get the delivery to the customer’s doorstep. Coordination and communication with the customer is vital for getting the order safely to its destination.
6. Returns management (reverse logistics)
If your customer is unhappy with their order and wants to send it back for a refund or exchange, the returns process is also an important part of end-to-end logistics. E-commerce stores must have a streamlined returns process in place so customers can easily initiate the returns process. Warehouses must thoroughly inspect and restock refunded items, and update inventory management systems to update product availability.
7. Customer service
Customer service solutions also fall under the banner of end-to-end logistics. Communication channels should be easy to find and managed so that inquiries can be solved quickly. Feedback and problem solving can help businesses identify and improve the entire end-to-end logistics cycle, and provide customers with a positive post-purchase experience.
While these are the main processes e-commerce businesses will regularly engage with, there are many more which help businesses optimise, scale and run their day-to-day business. Data analytics, optimisation, technology integration, security, fraud prevention and sustainability practices are all important parts of end-to-end logistics.
End-to-end logistics benefits: streamlining the supply chain
Each step in the end-to-end logistics cycle is incredibly important. To be successful, businesses have to make sure each cog in the machine moves seamlessly into the next, creating an efficient and streamlined set of processes that customers can rely on. To do this you need to constantly evaluate your E2E processes. The benefits of optimising end-to-end logistics are:
Improved efficiency and reduced redundancies
By narrowing in on areas of improvement across the supply chain you can improve the entire end-to-end logistics cycle. The goal of regularly evaluating and optimising distribution, warehousing, transport, etc is to make the entire process from start to finish efficient and cost effective. Removing any redundant or slow processes will impact your bottom line.
Cost efficiency and faster order fulfilment
As we just mentioned, a well-oiled supply chain will help you cut costs and fill orders faster. Streamlining logistics processes can lead to cost savings through better resource utilisation, reduced inventory carrying costs, and optimised transportation routes. It helps in reducing order processing and fulfilment times, leading to quicker delivery to customers. This can enhance customer satisfaction and loyalty.
Enhanced visibility across the supply chain
Better supply chain visibility is good for you and your customers. Implementing advanced tracking and monitoring systems provides real-time updates into the supply chain and status of customer orders. This allows you to make better decisions and proactively address issues.
Better customer service and satisfaction
When it comes down to it, it doesn’t matter how great your product is if your end-to-end logistics management is not up to scratch. Late deliveries, damaged shipments, and broken processes will all result in negative reviews and will hurt your businesses. Monitoring and improving upon your supply chain processes at every step will increase customer satisfaction and retention.
What technologies are driving end-to-end logistics innovation?
Throughout this article we have mentioned various technologies and how they are playing an increasingly vital role in smooth E2E operations. Integrating digital platforms and software into your supply chain helps automate a lot of key processes, speeding up the supply chain and helping you better allocate resources. Some important tools to consider are:
- Enterprise Resource Planning (ERP) Systems: These manage and streamline the core business processes of an organisation, including supply chain, procurement and sales.
- Warehouse Management Systems (WMS): Streamlines all areas of warehouse management, such as picking, packing, shipping and inventory tracking.
- Transportation Management Systems (TMS): Helps companies manage the logistics associated with the moving physical goods.
- Order Management Systems (OMS): Tracks all information and processes associated with orders, including inventory management and fulfilment.
- E-commerce Platforms: Helps e-commerce vendors build an online space to market and sell your goods or services. Has options to integrate a number of logistics software and tools for easier E2E management.
- Track and Trace Systems: Helps businesses keep an eye on their inventory as it moves through the supply chain.
- Route Optimisation Software: Helps carriers and couriers find the most optimal way to deliver their goods.
All of these software systems (and many others) are integrated into the end-to-end logistics cycle to provide accurate, up-to-date and automated processes that keep the supply chain moving smoothly.
As logistics technology continues to grow, the Internet of Things (IoT) and Artificial Intelligence (AI) are becoming more valuable in supply chain logistics. IoT devices like GPS trackers and RFID tags enable real-time tracking of goods, vehicles, and inventory throughout the supply chain. Smart sensors and robots enhance warehouse automation, and IoT sensors on vehicles and equipment can collect data on usage and performance. AI algorithms can then analyse this data to predict when maintenance is needed, reducing downtime and preventing unexpected breakdowns.
AI can also better predict demand patterns using historical data and market trends, allowing for improved inventory management decisions. AI-powered chatbots assist in customer service and order processing, providing quick responses to inquiries, tracking orders, handling routine tasks, and improving customer satisfaction.
When looking to the future of logistics, it’s clear that there is a move towards greater integration, sustainability and state-of-the-art tech innovation. Supply chains will be even more tightly integrated, data-driven and optimised for speed and cost savings, leading to greater efficiency. There will be more focus on reducing emissions and waste, and automation will remove the need for humans to perform mundane and repetitive tasks. Embracing the future of end-to-end logistics will give e-commerce stores a huge strategic advantage in terms of efficiency, scalability and customer retention.
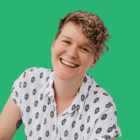
Emily Browne is a writer for ShippyPro who blends her passion for writing with an interest in all things e-commerce. Emily strives to make complex topics more digestible, proving that the world of logistics isn't as confusing as it sometimes feels! Her expertise in supply chain management, coupled with a knack for storytelling, helps readers navigate the complex world of e-commerce and shipping.