Warehouse Order Picking: Optimise Order Fulfilment

The importance of technology within e-commerce has made warehouse picking and packing a key area of optimisation within order fulfilment. Whether automated or manual, batch or wave; there are many ways the warehouse picking process can be improved to find the best system for your business and keep customer orders flowing.
What is warehouse picking?
Warehouse picking is the process of preparing orders in the warehouse or distribution centre before sending them out for delivery to the customer. Picking is a crucial part of e-commerce and order fulfilment and requires accurate technology and labour-focused processes to maintain accuracy with every order.
The warehouse picking process often involves a warehouse worker using equipment such as handheld devices, scanners and picking carts to locate and “pick” the items from designated locations within the warehouse. These items are then packed and prepared for shipment to the customer.
Why is warehouse picking so important?
Within a warehouse or distribution centre the picking process is a key element to a successful fulfilment operation. Accurate warehouse picking is essential to ensure that customer orders are accurately and efficiently fulfilled. If they are not, this can create serious problems for the e-commerce business and their level of service.
Large warehouses require good organisation and high-tech equipment to locate individual items quickly and accurately. Effective warehouse picking plays a vital role in the supply chain so that customer expectations are met and orders are fulfilled. Optimising this process can provide many benefits for the warehouse and the businesses that use them, including:
- Increased efficiency: Optimised warehouse picking processes reduce the time and effort it takes to fulfil customer orders which results in faster order processing and shipment.
- More accurate inventory management: Using tools that keep track of inventory levels during the picking process can make sure stock is replenished in a timely manner and is maintained accurately. When a product is out-of-stock, it’s very important for that update to be relayed back to the customer as quickly as possible, and that new inventory can be ordered quickly.
- Better customer satisfaction: Optimised warehouse picking picks, packs and ships orders quickly and accurately which can lead to increased customer satisfaction and loyalty.
- Reduced costs: Efficient and accurate picking helps minimise labour costs, optimises inventory and reduces the time it takes to fulfil orders which can lead to more orders being fulfilled. All this results in cost savings for the warehouse.
Warehouse order picking methods
From an outsider perspective, warehouse picking seems like a simple affair — order comes in, pick, pack and ship. However there are several types of warehouse picking methods that change depending on the size of the orders or the layout of the warehouse. Here are a few of the most common picking methods:
Wave picking
Wave picking is a way of processing orders by grouping products based on different criteria. For example, you can group orders by carrier, customer or the packaging you need. Whatever you choose, products are picked in a predetermined sequence. This method is most ideal for warehouses with a high volume of orders.
When orders are prepared using this method, they will be carried out within a specific time frame. Each wave of products is usually made within 45 minutes and two hours, depending on the size of warehouse and the location of the products.
This is a method that maximises the collection and delivery of orders as it is possible to coordinate several waves to comply with the distributor’s shipping schedule. The predetermined nature of wave picking also means that the inventory can be resupplied in advance, which improves inventory management.
However, a disadvantage of wave picking is that after all the items have been collected from the shelves during the wave, they will still need to be sorted, processed and delivered to the customers who ordered them.
Batch Picking
If a warehouse decides to use batch picking, they will group together multiple orders into a “batch” to be picked simultaneously. This allows the picker to make fewer trips to the same location in the warehouse, which saves time and increases efficiency. Orders can be collected based on various different criteria.
Batch picking helps reduce operator traffic in warehouse aisles during order preparation. It can also optimise delivery time as orders can be grouped together based on destination. Batch picking, however, is best for warehouses that store many items with a similar size, weight or function. If the inventory is too varied (or ships all over the country) batch picking might not be helpful. Warehouses also need a layout that allows for the movement of large groups of items, pallets or boxes.
Piece picking
In piece picking, individual items are picked and packed for shipment one at a time. It is the most basic and straightforward warehouse picking method, and is most ideal for smaller warehouses with less order volume. Piece picking can be done manually or by machine, and it can increase order accuracy but can also be very time consuming, which is why it does not work well for large warehouses with a lot of inventory.
Many warehouses will automate piece picking to make the process more efficient and accurate. This helps reduce labour costs, increase reliability, reduce errors and speed up the picking rate.
Zone picking
In this picking method, the warehouse is divided into different zones, and each specific zone will have a picker assigned to it. Each picker will be responsible for locating all the items from that zone for a particular order, and then the orders are combined for shipment. Similar to zone picking is cluster picking, where warehouses will cluster items that are frequently ordered together.
Zone picking decreases congestion around the warehouse, as movement will be limited to each individual zone. It also helps keep the inventory organised and increases efficiency as warehouse staff will be able to find what they need in each zone.
However, zone picking ( or cluster picking) can become complicated if you receive multi-part orders which contain items spread out across different zones. You will still need to correctly combine orders for shipping. Furthermore, demand might be inconsistent across zones which will leave some warehouse staff extremely busy, while others wait all day for work.
Pick and pack
Small warehouses with limited space will tend to opt for the pick and pack method. In this method the picker not only finds the items, but they will also package them for shipment. This method saves on labour costs but is not feasible for large warehouses with hundreds of orders a day.
Automated warehouse order picking
Automated warehouse order picking is when warehouses employ automated technologies and systems to fulfil customer orders by selecting and gathering the required items from designated locations within a warehouse. Examples of automated order picking systems include robotics, conveyor systems, automated guided vehicles (AGVs) and advanced software algorithms. Automated systems help warehouses increase efficiency, reduce labour costs, save money and improve accuracy.
5 ways to optimise ware picking for e-commerce
Technology has allowed warehouses to become more efficient, accurate and competitive. Barcode scanners, RFID (Radio Frequency Identification), warehouse automation and voice-activated picking can significantly improve accuracy and speed up the picking process. However there are plenty of ways to optimise warehouse picking alongside improved tech and warehouse trends. Here are five ways warehouses can optimise their picking processes.
Implement a warehouse management system (WMS)
Most modern warehouses need the right software to manage and monitor the movement of orders around the facility in real-time, which is where WMS systems come in. These systems are key to developing a competitive edge, and help minimise labour costs, increase accuracy and improve customer service. WMS systems benefit warehouses by providing real-time inventory data, automating pick-list generation and data for performance analysis.
Many e-commerce platforms use third-party logistics (3PL) to leverage warehouses in order to pick, pack and deliver their goods. For this purpose there are three types of WMS to use; Standalone Warehouse Management, Supply Chain Execution Modules and Integrated ERP. Which one you choose depends on function, warehouse size, cost and customer needs.
Optimise picking paths
Much like delivery optimisation which relies on technology to calculate the most efficient route from A to B, the same can be applied to picking paths. Some warehouses are absolutely enormous, and therefore picking paths need to be made as short as possible to improve efficiency.
There are a few ways to streamline picking paths. One example is to use a pick-to-light system which uses LED lights to illuminate the most efficient path to a product. Once the product has been picked, the operator can then light the path to the next product, and so on. Another example of picking path optimisation is to use software that maps, calculates and displays the shortest path necessary to retrieve all the SKUs requested by a customer.
Implement slotting
Slotting refers to grouping inventory based on their popularity and frequency of order. Popular products will all be grouped together close to the packing area to reduce pick time and minimise the distance travelled. Slotting is similar to batch or zone picking, as it uses key processing data to group inventory based on sales and stores it closest to the packing area for increased efficiency.
Further benefits of warehouse slotting include faster picking with less errors, opportunities for increased storage capacity and reduced carrying costs.
Improve staff training
While technology can get you far, building a team of dedicated and motivated warehouse staff will get you even further. Proper training for warehouse staff is essential for optimising the warehouse picking process. Staff training should include proper picking techniques, how to operate equipment correctly and up-to-date safety procedures. Furthermore, team building exercises and mentor programmes can help boost morale and prevent high staff turnover, which can become expensive.
Implement a quality control processes and performance analysis
Being able to consistently analyse your processes and update/optimise functions will keep your warehouse competitive and running effectively. Regular analysis helps identify any areas of improvement and quality control processes can help catch errors before orders are shipped. This reduces the time and cost of fixing errors once they’re out.
Warehouse picking is one of the six fundamental warehouse processes: receiving, put away, storage, picking, packing and finally shipping. When all six of these functions are optimised, warehouses can improve accuracy, efficiency and reduce errors which all leads to better customer satisfaction and a successful fulfilment process.
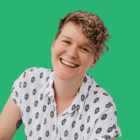
Emily Browne is a writer for ShippyPro who blends her passion for writing with an interest in all things e-commerce. Emily strives to make complex topics more digestible, proving that the world of logistics isn't as confusing as it sometimes feels! Her expertise in supply chain management, coupled with a knack for storytelling, helps readers navigate the complex world of e-commerce and shipping.