Logistique lean : qu'est-ce que c'est et comment réduire les déchets dans la logistique ?

La logistique lean est une approche de travail qui vise à améliorer la logistique d’entreprise en optimisant le flux des processus logistiques et en réduisant les gaspillages le long de la chaîne d’approvisionnement.
Cette approche s’appuie sur le lean thinking, la philosophie à l’origine de la lean manufacturing (dans les contextes de production) et de la lean logistics (dans les contextes logistiques).
Dans cet article, nous verrons en quoi consiste l’approche « lean », quels sont les avantages de la logistique lean et les points clés pour gérer les activités logistiques avec une mentalité lean, afin d’accroître l’efficacité globale de l’entreprise.
Logistique lean : définition et histoire
La logistique lean est une approche stratégique de gestion de la chaîne d’approvisionnement fondée sur un ensemble de techniques et de stratégies destinées à réduire le gaspillage en éliminant tous les processus qui n’apportent pas de valeur au flux de travail de l’entreprise.
En pratique, la logistique lean repose sur les principes du lean thinking et de la production lean, avec pour objectif de maximiser l’efficacité de l’entreprise, de la production jusqu’au consommateur final.
Découvrons l’origine de cette philosophie et la façon dont elle a été appliquée au secteur logistique.
Origines de la logistique lean
Cette approche trouve son origine dans la philosophie développée par Toyota dans le Japon des années 1950. C’est là qu’est né le lean thinking, qui a permis à Toyota de surmonter d’importantes crises économiques.
Dans l’après-guerre, Toyota traversait une période difficile : la concurrence occidentale féroce et les ravages de la Seconde Guerre mondiale avaient réduit les ressources de l’entreprise.
Toyota entreprit alors de développer un système de production novateur pour optimiser l’efficacité et réduire les gaspillages.
Les fondements du lean thinking reposent sur :
- l’élimination des gaspillages (muda en japonais) ;
- la production à la demande (pull) ;
- la production en flux continu (flow) ;
- l’amélioration continue (kaizen) et le respect des personnes.
Le Toyota Way :
- identifie plusieurs types de gaspillages : surproduction, temps d’attente excessifs, transports inutiles, etc. ;
- grâce au concept pull, stipule que la production n’a lieu que lorsqu’elle est demandée par le client ;
- avec le terme flow, fait référence à une production continue et sans interruption, minimisant les temps morts entre les étapes ;
- avec le concept kaizen, poursuit le progrès continu en impliquant tous les niveaux de l’organisation.
En pratique, chaque collaborateur est considéré comme un élément essentiel capable de transformer les performances de l’entreprise. Cette vision a instauré une relation de confiance solide entre l’entreprise et ses employés, contribuant à forger un objectif commun.
Associée à des stratégies d’optimisation des flux de travail et de réduction des gaspillages, cette approche a permis à Toyota de rester compétitive.
Le succès du Toyota Production System (TPS) a favorisé la diffusion du lean thinking dans de nombreux secteurs à travers le monde.
D’abord cantonnées à l’automobile, les stratégies lean se sont progressivement étendues à d’autres domaines, couvrant aussi bien l’intralogistique, la logistique externalisée, la logistique du dernier kilomètre que l’ensemble de la supply chain.
Qu’est-ce que l’approche lean ?
L’approche lean applique la pensée lean à tous les domaines de l’entreprise ; elle vise à supprimer les gaspillages en créant des processus standardisés avec le concours du personnel.
En suivant les pratiques mises au point par Toyota, de nombreuses entreprises ont adopté cette méthode, transformant non seulement leurs processus opérationnels mais également leur culture d’entreprise – valeurs et règles.
Le lean thinking est donc le socle de la lean manufacturing, axée sur la réduction du gaspillage et l’optimisation de la production, comme de la lean logistics, qui applique la pensée lean à la chaîne d’approvisionnement.
Les fondements de la méthodologie lean
Womack et Jones ont analysé le modèle Toyota et mis en évidence cinq principes fondamentaux :
- Value ;
- Map ;
- Flow ;
- Pull ;
- Perfection.
Examinons-les.
1. Value
Pour définir correctement la valeur d’un produit ou d’un service, il faut l’envisager du point de vue du client et concentrer les activités sur la création de cette valeur tout en évitant le gaspillage.
Seules certaines activités ajoutent de la valeur au produit pour le client final. Déterminer cette valeur est crucial parce qu’elle explique pourquoi le client est prêt à payer.
Questions clés :
- Qu’est-ce qui justifie l’existence de l’entreprise ?
- Quels sont les besoins et attentes des clients ?
- Quelles activités n’ajoutent pas directement de valeur pour le client ?
2. Value Stream Mapping
La cartographie du flux de valeur est essentielle pour analyser et optimiser le flux de travail, en supprimant les activités sans valeur ajoutée et en simplifiant le processus.
Cette étape révèle également les muda, c’est-à-dire les gaspillages : surproduction, manipulations inutiles, erreurs administratives, étapes superflues, etc.
Questions clés :
- Quelles sont les étapes critiques du processus ?
- Où apparaissent les plus grands retards ou gaspillages ?
- Comment simplifier le processus en retirant les étapes sans valeur ajoutée ?
3. Flow
Le troisième principe concerne l’optimisation du flux de travail afin de réduire le temps de cycle et de le rendre aussi fluide que possible.
Le manque de synchronisation entre les activités ralentit le processus, affectant la production comme la logistique. Il est donc essentiel d’éliminer tous les obstacles qui peuvent freiner ou bloquer le flux.
Questions clés :
- Comment réduire les temps de cycle ?
- Où se produisent les goulots d’étranglement ?
- Quelles zones pourraient améliorer le flux global ?
- Comment relier les activités créatrices de valeur ?
4. Pull system
Le système pull consiste à produire uniquement ce que le client demande réellement, évitant la surproduction et les stocks excessifs. Le terme pull (« tirer ») signifie ici déclencher : c’est le client qui déclenche toutes les activités. Il s’oppose au système push, où l’entreprise pousse la production.
Questions clés :
- Comment synchroniser la production avec la demande réelle ?
- Comment éviter surproduction et stocks excédentaires ?
- Quels indicateurs doivent déclencher la production ?
- Comment déclencher les activités ?
5. Perfection
La perfection renvoie au kaizen : l’amélioration continue obtenue grâce à la collaboration de tous. Il est important de reconnaître les progrès, sans jamais cesser de rechercher l’excellence. La poursuite constante de l’amélioration élimine encore plus de gaspillage et perfectionne tous les processus.
Questions clés :
- Quand peut-on se dire satisfait ?
- Comment améliorer continuellement les processus ?
- Quels défis faut-il relever pour atteindre un niveau supérieur ?
- Comment encourager l’innovation et l’apprentissage continu ?
Après avoir passé en revue les cinq principes lean, voyons comment ils permettent de gérer efficacement la logistique.
Points clés de la logistique lean
La pensée lean s’applique à tout secteur, y compris la logistique. L’adopter permet d’identifier et d’éliminer tout ce qui ralentit les processus de la chaîne d’approvisionnement, en tirant parti de stratégies telles que les expéditions LTL et FTL, les stratégies multi-transporteurs, le cross-docking, la direct injection, etc.
En nous basant sur les cinq principes, voyons lesquels appliquer pour bâtir une chaîne d’approvisionnement en logistique lean.
En logistique lean, on applique ces principes de base, mais selon les besoins spécifiques de la chaîne, ils peuvent être précisés ou adaptés.
Les principes suivants ne sont donc que quelques-uns de ceux que l’on peut retenir. Ils peuvent varier ; il n’existe pas de liste unique. L’essentiel est d’appliquer les principes du lean thinking à la gestion logistique pour éliminer les gaspillages, fluidifier les flux et améliorer les opérations.
Stratégies à mettre en place :
- Identifier la valeur du produit
- Éliminer les gaspillages
- Créer un flux continu
- Fournir les biens uniquement sur demande
- Rechercher la perfection
1. Identifier la valeur du produit (Value)
Le premier principe lean consiste à déterminer la valeur d’un produit ou d’un service du point de vue du client.
Il est donc essentiel de comprendre ce que le client perçoit comme valeur dans le domaine logistique. Cela peut inclure :
- des délais de livraison rapides,
- une gestion des commandes précise,
- une flexibilité dans les livraisons, etc.
Une gestion optimale des expéditions passe par une stratégie qui élimine le gaspillage. Pour réduire les délais, améliorer la précision ou accroître la flexibilité, il faut supprimer toutes les activités sans valeur pour le client et qui ne font que ralentir les opérations.
Comment procéder ?
Un soutien précieux vient des KPI logistiques, indicateurs indispensables pour mesurer l’efficacité des activités.
2. Éliminer les gaspillages (Value Stream Mapping)
Comme dans la pensée lean, l’objectif principal est d’éliminer les gaspillages :
- réduire les temps d’attente,
- éviter les mouvements inutiles,
- optimiser les itinéraires de transport,
- réduire les stocks excédentaires.
Une cartographie du flux de travail clarifie la dynamique des expéditions et permet d’identifier les points critiques, les gaspillages et les pistes d’amélioration.
Comment les supprimer ?
Les technologies de gestion logistique sont de plus en plus évoluées ; les données – des stratégies marketing à l’optimisation d’entrepôt – ouvrent la voie à de nouvelles stratégies pour fluidifier les flux.
ShippyPro, par exemple, simplifie la gestion des expéditions : création automatique d’étiquettes avec Label Creator, suivi (Track & Trace) et gestion des retours via Easy Return. Intégrer ShippyPro dans une perspective lean aide à réduire le temps et les ressources gaspillé·e·s par une gestion manuelle.
3. Créer un flux continu (Flow)
La logistique lean vise à instaurer un flux de matières continu et sans interruption dans toute la chaîne d’approvisionnement. Cela suppose de réduire les temps d’attente, d’optimiser les processus et de synchroniser les activités pour éviter les retards.
Comment y parvenir ?
L’analyse des KPI d’entrepôt est un excellent outil pour examiner le centre névralgique des expéditions.
4. Fournir les biens uniquement sur demande (Pull)
Appliquer le principe pull signifie fournir la marchandise uniquement quand le marché la réclame, ce qui évite la surproduction et maintient des niveaux de stock bas.
Comment faire ?
Ici encore, des outils liés à une bonne gestion d’entrepôt soutiennent l’analyse pour améliorer la production et donc les expéditions. Divers WMS offrent de nombreux avantages d’automatisation et peuvent gérer chaque secteur de l’entreprise.
- Rechercher la perfection (Perfection)
Le principe d’amélioration continue s’applique aussi à la logistique : les organisations cherchent sans cesse à perfectionner leurs processus logistiques pour accroître efficacité, flexibilité, fidélisation clients et réduire les gaspillages.
Comment l’atteindre ?
Une bonne stratégie consiste à impliquer fournisseurs, partenaires et surtout le personnel. Une collaboration étroite entre tous les maillons de la chaîne est indispensable pour garantir une gestion fluide, sans entraves et en quête permanente d’efficacité.
Conclusions : les avantages de la logistique lean
Appliquer la logistique lean présente de nombreux bénéfices : réduction du gaspillage, augmentation de l’efficacité opérationnelle, amélioration de la qualité de service et meilleure capacité d’adaptation à la demande.
Optimiser la chaîne d’approvisionnement réduit les gaspillages et accroît ainsi le marge bénéficiaire.
Par ailleurs, le client ne perçoit pas la valeur des gaspillages générés le long de la chaîne ; l’optimisation des flux logistiques rehausse donc sa satisfaction.
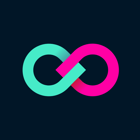
ShippyPro est le logiciel d'expédition complet pour la vente au détail en ligne et hors ligne. Avec ses fonctions de création d'étiquettes, de suivi et de traçabilité, de retour facile et d'analyse, notre logiciel simplifie vos opérations d'expédition. ShippyPro s'intègre avec plus de 180 transporteurs et 80 canaux de vente, ce qui le rend compatible avec une large gamme de produits et de cas d'utilisation.